SERIES
Bend series
Tee series
Flange series
Reducer series
Simmer the bent pipe ser
Wear-resistant pipe fi
Plant accessories series
Ripple compensator seri
Pipe expander
Cleaner series
Piping support series
Head cap
Pipe series
Insulation series
Series of anti-corrosion
Concrete pump accessories seri
Plastic Lined Pipe Series
Surfacing machine / wire drawi
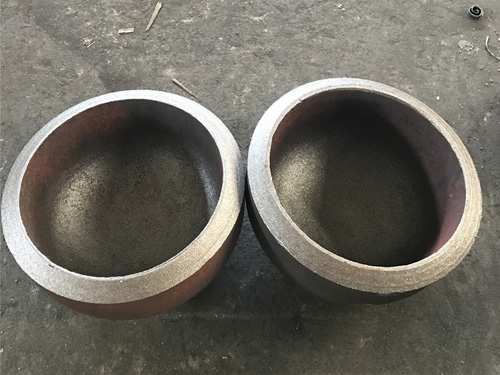
Pipe cap
The cap is also known as the head, block, head, tube cover and head, welded to the pipe end or installed in the pipe end to cover the pipe fitting. Used to seal the pipeline, the function is the same as the pipe.
The form of the blind plate is close, except that the blind plate can be disassembled and the welding cap is not disassembled. The cap includes the design of the convex tube cap, conical shell, variable diameter section, flat cover and constriction.
The cap includes a hemispherical tube cap, an oblong cap, a disc cap and a ball cap. From the point of view of force, the cap of the convex tube is gradually not good, but from the difficulty of making it, it is gradually made.
Stainless steel: 304 304L 316 316L 321 2520 310, 317, etc.
Size: DN15-48 ")
Wall thickness: SCH5 - SCH160
Standard: ASME DIN JIS BS GB/T JB SH HG, specific as follows: GB/T12459-2017, GB/T13401-2017, ASME B16.9, SH3408,
SH3409, HG/T21635, DL/T695, SY/T0510, DIN2617
USES: water, beverage, beer, food, petrochemical, nuclear power, machinery, medical equipment, chemical fertilizer, shipbuilding, waterproof treatment, pipeline, etc
Packing: wooden cases and cartons
The r of the disc cap is not spliced, it will be thin and high stress.
When splicing the weld direction requires only radial and circular direction. A large cap may then cancel this requirement. The distance of splicing should be required to be greater than 3 delta and not less than 100mm (welding thermal zone is a high stress zone, and the chemical composition of the area will be burned. Therefore, to avoid the high stress zone, the region is related to the thickness. According to practical experience, the stress attenuation length is greater than 3 delta and not less than 100mm. But refrigeration equipment is difficult to meet this requirement, has its particularity.
After splicing the sealing head, the welding seam should be 100% or ultrasonic testing, and the qualified level will go with the equipment shell. The post-forming seam inspection level, proportion and equipment shell are the same, high waste.